GEA opened the doors of its new 1500-sqm Technology Center (XLAB) in Biedenkopf-Wallau for the first time on March 20. From now on, the new XLAB will be available to customers for product testing and training. During the opening ceremony, guests had the opportunity to be the first to get acquainted with the new location and technological developments of the internationally operating group for the food processing industry.

“We are very excited to open our new Technology Center, after a short six-month construction phase. With the XLAB, we are taking product testing for our national and international customers to a whole new level. A special feature is the new 500-sqm air-conditioned hall, which can be cooled down to freezing point and enables customer tests under realistic conditions,” says Moritz Krunke, Managing Director of GEA’s Wallau site.
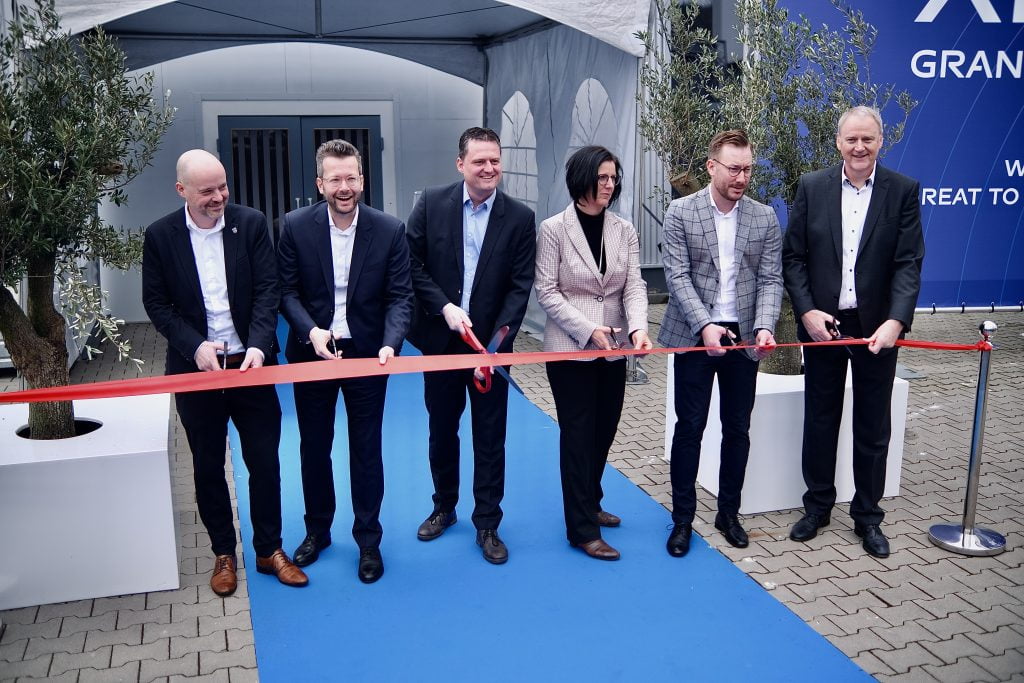
During the opening week, automation, digitization, sustainability, as well as training and performance support workshops will be offered to customers. Plant tours and live demonstrations on the slicing and packaging line, SmartPacker and CutMaster round off the program. Individual machines and complete, highly digitalized production lines are on display on the exhibition floor, and the business unit’s entire product portfolio is available. This includes technically complex thermoforming and vertical packaging machines, high-speed cutting and loading systems for meat, sausage, ham/bacon, cheese, frozen foods and vegetables, as well as highly flexible bowl cutters for the production of sausages, cheese, fish and meat substitute products. In addition, this business unit of GEA offers solutions for the production and packaging of lollipops and other confectionery and food products. The XLAB combines expertise from across the GEA business unit at one location.
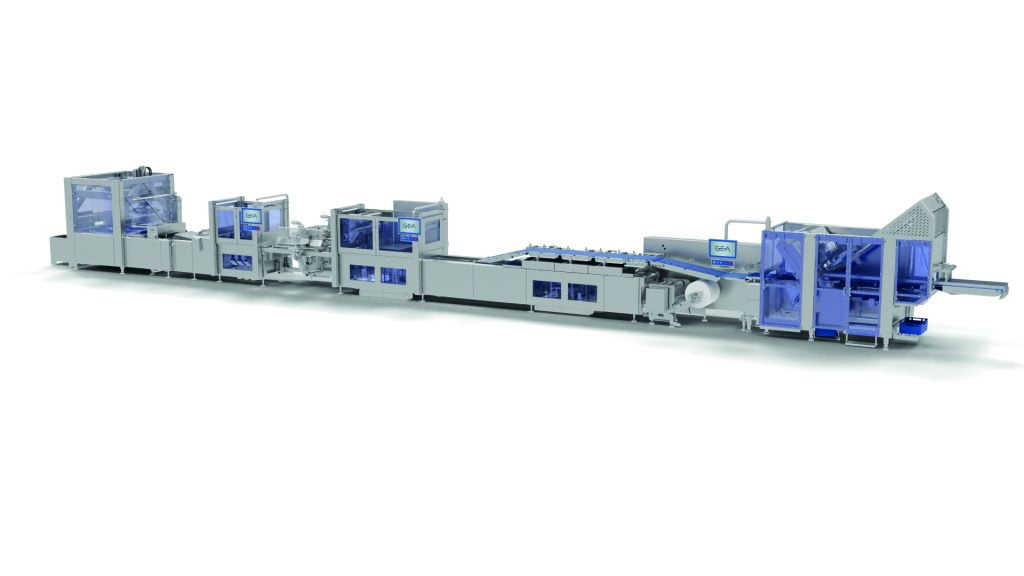
GEA offers technology transformation “Our new Technology Center underscores our partnership-based customer relations on a national and international level. Together with our customers we develop tailored solutions that will play a decisive role in the technological transformation of the respective production area,” adds Jörg Kuhn, Vice President of the Slicing & Packaging Business Unit.
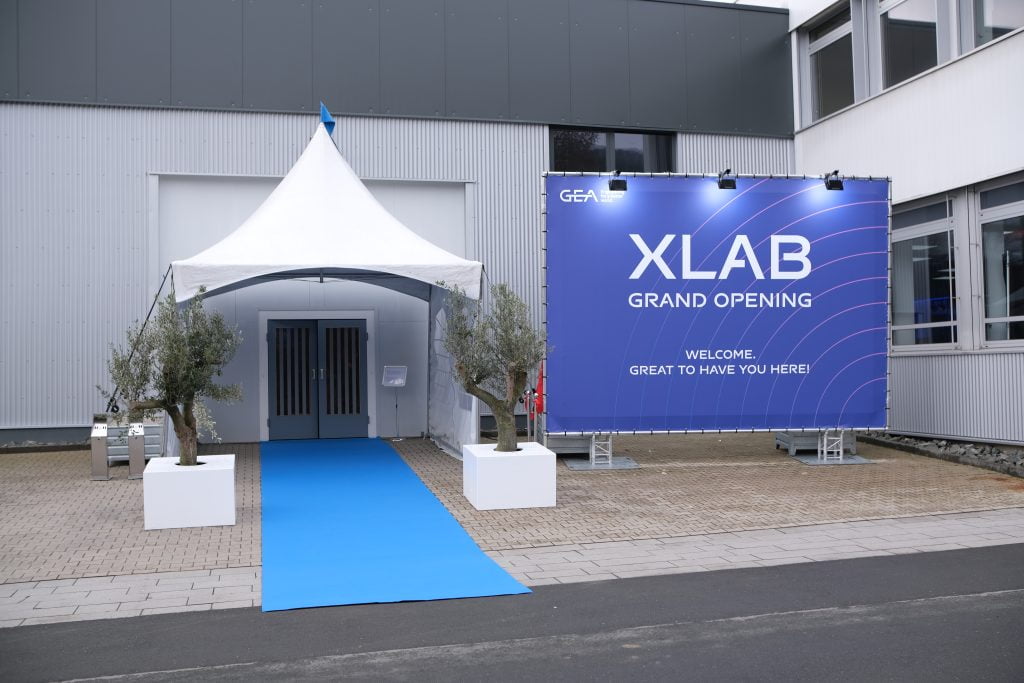
GEA has been active in the food segment for many years and has since developed into a full liner that offers expert knowledge to support its customers throughout the entire process. GEA is not only a supplier, but also a consultant for customers just entering the industry. These are integrated into the processes and planning at an early stage. In addition to consulting, GEA stands out as a full-line supplier of machines for the entire process line, automation and software, which is a huge plus in terms of efficiency.
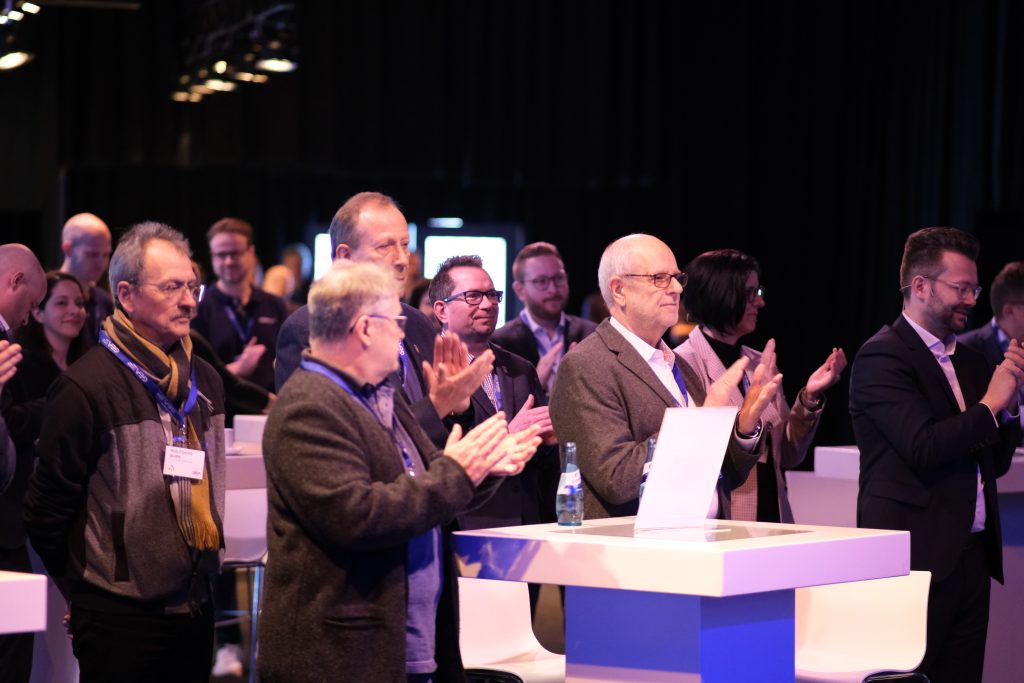